Supplier quality rating report | Supplier scorecard and performance
Supplier quality rating report is a document describes supplies quality, compliance and overall performance of each supplier to compare excellent performance and rating individual supplier. It is base document for supplier’s acceptance or rejection for future supply.
Overview
Supplier quality rating is enables organization to determine supply decisions. These decisions can includes identifying excellent supplies for specifically designed, quality and services. It may also for determine new exploration of supplies, which could beneficial than existing suppliers.
The supplier quality rating is initial process that impacts on critical decisions. The base analysis of supplier quality rating will help to determine which supplier will provide conformity products for application requirements.
Why supplier quality rating is important?
- Improvement and effectiveness of procurement processes are assessing by the quality and reliability of suppliers.
- Identifying excellent performance of suppliers, and new sources to meet existing and future requirements. This is initial requirements for continual improvement.
- It will help to focus on suppliers, which are gives us the excellent performance.
- Every supplier’s strength and weaknesses should be reviewed for continuous improvement.
- The supplier quality rating provides specific models to evaluate supplier performance by reliable methods.
The quality rating of suppliers is conduct for all kinds of supplies. Those may include consumable goods, raw material or in process used. The poor quality of materials can damage manufacturing processes or resources as results reduce performance of equipment utilization. In case of lower quality of raw materials may trigger huge issues at on final product or end application compliance. It may cause loss of customers.
How to calculate supplier quality rating?
Supplier quality rating is calculated on based of standard quality criteria. it is very important to identify some affected factors that increasing challenges for defines to sustain standard quality criteria. Some of the affected factors or key questions are following:
- How much supplier quality rating (SQR) in percentage is acceptable for you?
- What should be criteria of the reject material?
- How much quantity / percentage rejections are acceptable?
- How much percentage of the material per lot is acceptable for you?
- What will be primary theme for the supplier unqualified for supply the material?
- What should be action for the rejection level reduces of your supplier?
- How you will promote to quality system maintain in its organization?
There are bunch of questions that impacts on the quality rating. But basically concept is clear, every supplier should be developed to provides quality materials to maintain supplies chain.
Rating and assessment
Supplier quality rating should have defined frequency and time bounds. You have to define sustainable frequency for the checking of supplier quality rating. Generally, organizations are generating reports on monthly, quarterly or half yearly. But Half and annual reports are not much effective, due to its makes complicated for identify lots and rejections where high level of quantity are in stock.
See example format of supplier quality rating report:
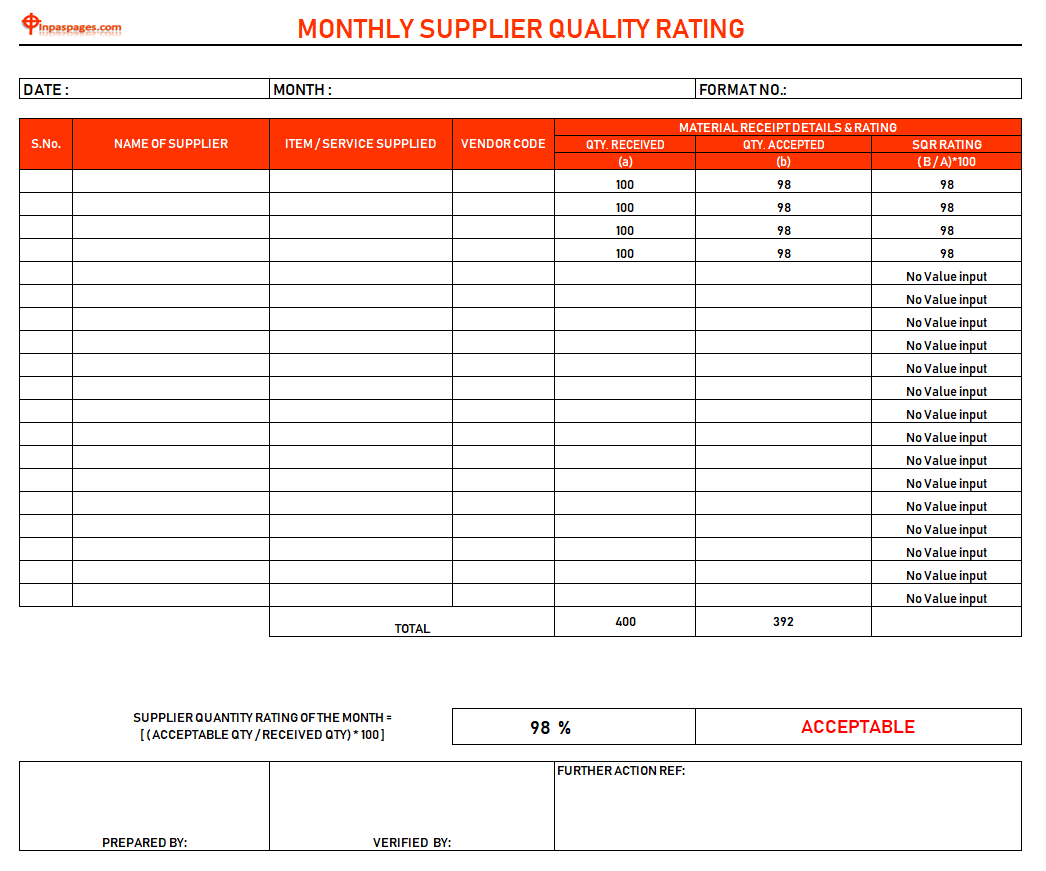
Pingback: Supplier Audit Checklist format for supplier internal quality audit
Pingback: Supplier Appraisal Form / Supplier Evaluation Form
Pingback: Supplier Development Plan / Supplier Development Program: Vendor Development