Supplier corrective action report | SCAR
A SCAR (Supplier corrective action report) is a document given to supplier for identify root causes of non-conformity with supplier’s supplies, system or services. A document defines information of corrective actions require to implement at supplier facilities by supplier end, it will eliminate future non conformance.
Overview to SCAR
According to International Standards supplier chain awareness & development, increase productivity can effect positive on the quality that is delivering. It will also financial chip product can possible to deliver by suppliers. ISO TS 16949 international standards also recommend the supplier chain, that need to update regular basic. mostly evaluation of each supplies for the maintain product quality which is used in production lines as raw materials.
For continual improvement of supplier chain, quality team conduct the internal audit at supplier’ facility. Which may include product quality, services and internal system of supplier’s facility. During the audit period in case any non-conformity found, audit team will raise non-conformity report. “When audit team auditing its own facility, it will have called “non-conformity report”, but when audit conducts at supplier’s facility, it will have called SCAR.
Two types situations are generating Corrective action reports:
- As results of supplier’s audit, some non-conformity can be found that should be fulfillment and commitment required from supplier. Supplier gives assurance it’s system is effectively established and maintained. All identified non-conformity are documented in corrective action report, that is “supplier corrective action report”
- Some products or services are purchased from supplier that not met the requirements of applications / product or any others reasons are non-conformity are raised by customers. Those kind of non-conformity are needs to comply in line with customer expected structural formats, which used in its internal system. The report format is also called “Corrective action report” is primary evidence of the compliance by supplier for the further actions of non-conformities are generated.
How customer will verify the report?
Customers are collects those reports for used for follow-up. Customers will takes the appropriate actions to measure impacts on processes, they are change for positive reflects on processes. As same the same side, suppliers are also takes actions in its internal system to subject of affected areas. It’s very important document that describes transparency of the suppliers should accurate.
Generally, customers are verifying the documents provided by suppliers. It’s may have related to its internal system change, product design & any process change. In case of any changes are require at customer’s end, that will verify it with procurement system. Procurement team will do change of technical sheet of raw materials, or any document change is require.
Before the any amendment or modification in internal system or design / layout changes that suppliers should be provide all the necessary details for enable on further actions. It’s very tough situation that are corresponding with supplier in case of non-conformity are affect the internal system or production lines to lucidity does matter.
Document: See example format of Supplier corrective action report:
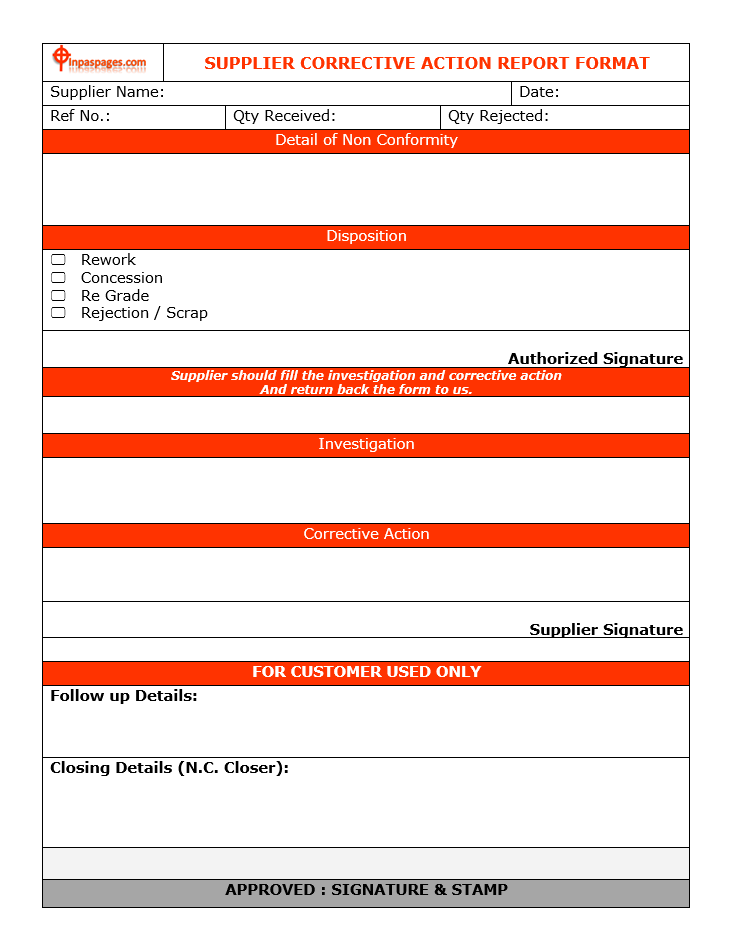