How to reduce devaluation of product
Devaluation of product is value of product reduce due to significant factors & reasons affecting product quality or enhance wastage.
Devaluation of product is hidden loss for organization; generally most small scale and middle scale industry are not concentrating on devaluation of product or not take enough try and steps to minimize or reduce devaluation of product during various manufacturing processes, storage of product and in-process activities, and the significant factors that directly affecting product quality, processes disturbance, improvement percentage of waste and scrap during processing materials etc.., needs to proper procedure to easier for concern management to monitoring on those activities and defined controls to handle process requirements & minimize it. The internal management system, deployment of proper work instructions, awareness and training to employee, standards system for raw materials purchasing and management of maintenance are major requirements to controls on devaluation of product, and the system should be effectively internal and externally ( sources of raw materials and bill of materials for production ) applicable and strong follow up required.
Best Practices: The devaluation of product’s main sources are scrap and wastage due to various reasons and factors and the scrap and wastage can possible to reduce or minimize percentage of wastage by implement best practices for the handling, storage of raw materials and in-process temporary storage and manage of product concern effective procedures, instructions of each of different types of materials, products sizes and specifications and identification of sources of reasons that scrap and wastage are raised significantly in manufacturing processes, in-process storage, handling the materials, quality and packaging. The process should be manage effectively to save most significant loss cost in production lines reason that focus on in-process scrap or devaluation of product due to rejected materials is a total loss of production labor, raw materials cost, handling charges and overhead costing raise significant material devaluation.
The significant factors and reasons that affecting product values on reduction of quality percentage, process losses raised and needs to effective actions to identification of factors and reasons that raising scrap & waste during storage, handling and manufacturing processes including packaging and dispatching materials. The actions needs to analysis of the reasons that generally scrap are generating & behind the devaluation of product. Generally below 7% industrial scrap acceptable, but if the more that 7% is significant loss of manufacturing unit that needs to proper controls through conducting analysis of scrap generating during manufacturing activities is help to determine actions to controls over processes that maximum scrap generating and help to reduction in scrap during various processes in manufacturing processes. See below picture is provided as example of scrap analysis are generally managed and identify sections where percentage of scrap generating by effective system, supervisor interactions in scrap calculation and monitoring to collecting data at each stage of manufacturing.
See picture: Scrap Analysis
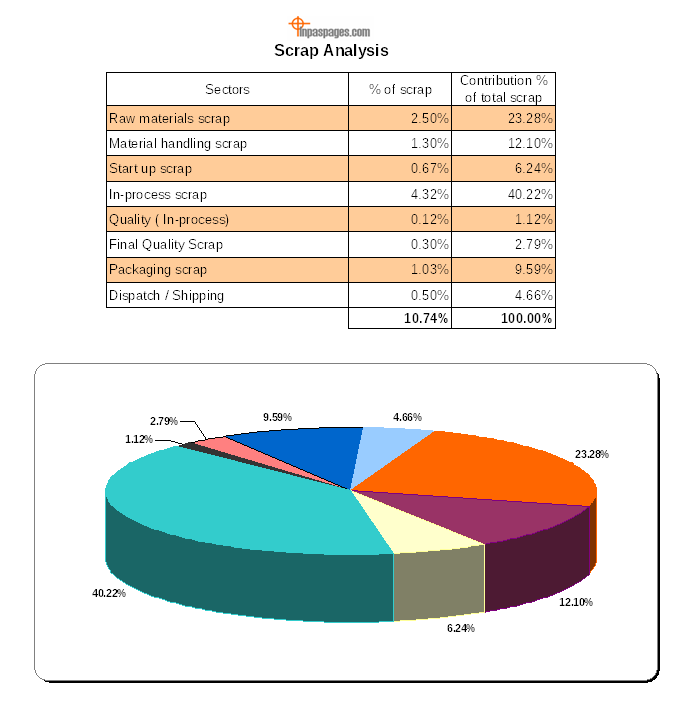
The process reviews and scrap analysis helps to determine particular section that generating significant percentage of scrape during its process that help to determine actions to reduce percentage of scrap generating, and manage sustainable processes to maintain tolerance to improve quality of product. But the section scrap analysis is not enough to manage proper actions that affecting factors, the processes and various acts are responsible for product devaluation are needs to identify in processes, see the specific reasons are generally responsible for devaluation of product:
- Raw materials defects: Improper staging of raw materials in raw materials storage areas and random storage that needs movement, handling and moving when needs raw materials for processing.
- Supplier defects: Supplier defects are comes with raw materials that became a product defects if the raw materials are not properly inspected but some defects are raised when the materials conducted for processing are managed in head of supplier defects.
- Process stages / manufacturing error: Due to improper handling of processes in manufacturing activities can raise defects, and this kind of defects are due to process stages & manufacturing.
- Measuring instrument, equipment, devices errors are significant error should must be controls by maintain calibration process accurately. The defects are raised when improper measurement counts of product that wrong materials cutting, wrong measurement handled for producing materials are significant loss of materials.
- Material change, process change mistakes are rarely raised during the material change or process change in manufacturing processes, the mistakes are occurred if the procedures or guidelines not considered or miss-communication
- Material devaluation due to machine, equipment or concern maintenance issues cause material rejections are considered and managed for analysis. This kind of issues are handled by managing proper maintenance activities, machine and equipment services as frequency defined, and timely required process verification should be maintained.
- To managing accurate analysis and identification of materials devaluation are some factors that affecting by human, human errors or operator mistakes are rarely occurred but important and serious issues for manufacturing unit, this types of mistakes are considered and needs to provides proper awareness training, guidelines for operations, manufacturing and supporting processes procedures in simple language to easier for understands & motivations are also effective to improvement of productivity in manpower.
- The materials stocks, product storage at locations should properly system and its activity are responsible for stocked materials values reduce, if the materials are stacked improper, long time storage and not properly handled by authority can devaluation product hence needs to care and effective system can reduce it.
The manufacturing processes and its concern activities are monitored by concern supervisors and its records reviews are maintained as per frequency by department management, and devaluation concern records are also maintained when occurred, The reviews are managed for the identification of reasons, verification of the records which are maintained in production lines and other supporting areas, the devaluation records are maintained by production manager or general manager for identification of sources of scrape percentage for reduction, the records concern the devaluation is maintained in lines are given as example, see picture below provided for education purpose:
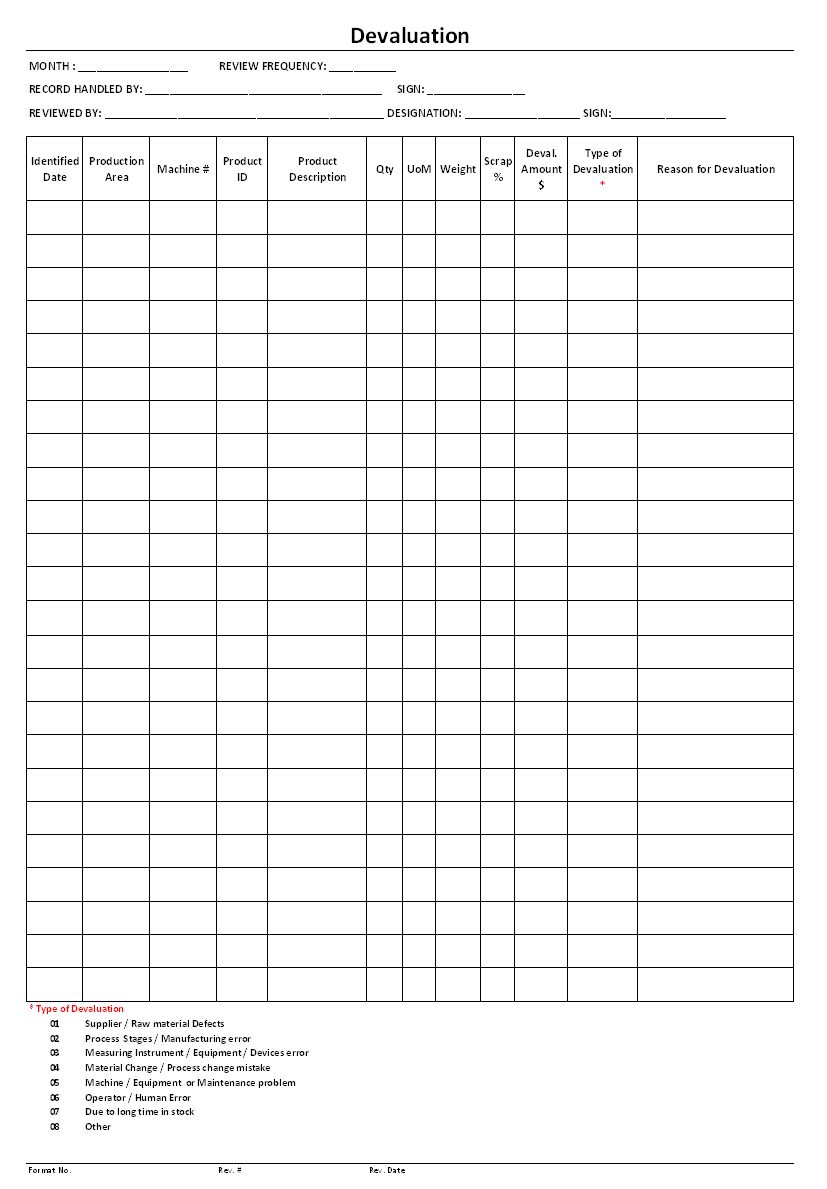
Devaluation format is used for recording concern activities, information that help to determine identified reasons sources and type of devaluation can minimized or eliminate from system, the format is covered identified location and areas, machine or equipment name where product devaluation is identified, product description in brief, total quantity affected, percentage of scrap and amount of devaluation that main part of the format that financially concern peoples can measure the devaluation, type of devaluation and reasons for devaluation are main field of the format and this information are collected and filled in this format for identify total product devaluation during the time period, on base of the records the analysis is conducted by concern authority and implement action plan to reduce devaluation.
—————————————————————————–
Download format in word document | Excel sheet | PDF format
Devaluation
—————————————————————————–