Quality system improvement action process
Quality system improvement actions and its process is describe requirement for improvement and actions on non conformity in system & documentation.
The purpose of the process of quality system improvement action is to describe the activities of internal system, customer internal system or supplier system’s identification non conformity, action plan preparation and implement for continual improvement, documentation & records are establish, monitoring on activities, controlling on the activities to prevent the non conformity in system, that can be in form of corrective actions and preventive actions. The system is covered the requirements of system improvements, action plans and actions on the non conformity occurred in system. Implementation of quality system to required establish of documentation system and documented procedure to instruct structural system and provided to working environment for continual improvement activities.
The system is covered all the part of the company that should concern with product quality, any employee in the company is the part of the quality system and responsible for implementation of quality system, concern department managers, in charges and finally management representative is prepared the requirements of the quality improvement and documentations. All the appropriate managers should ensure quality system implementation, corrective actions and preventive actions with effective implementation in their department, system implementation establishment, tracking, monitoring, identification of non conformity and controls over the system treats for effective implementation responsible of company if the system implementation within company, in case customer or supplier’s internal system implementation are need to aware appropriate requirements and system implementation action plans to control over non conformity.
The system coordinator is considered the system requirements and implementation plan is prepared, all the implementation steps are conducted on base of system is implemented at internal system, customer end or supplier internal system. System improvement id depends on the non conformity are found in the system with quality product concern relations, generally system improvement is conducted at:
- Customer’s Internal quality system
- Company’s internal system
- Supplier’s internal system
On base of the system implementation requirements, teams is considered the non conformity in the system and take the actions for the implementation of system, the actions can be in form of corrective actions and preventive actions to eliminate or minimize risk level or non conformity. See below picture for reference of the quality system improvement action form:
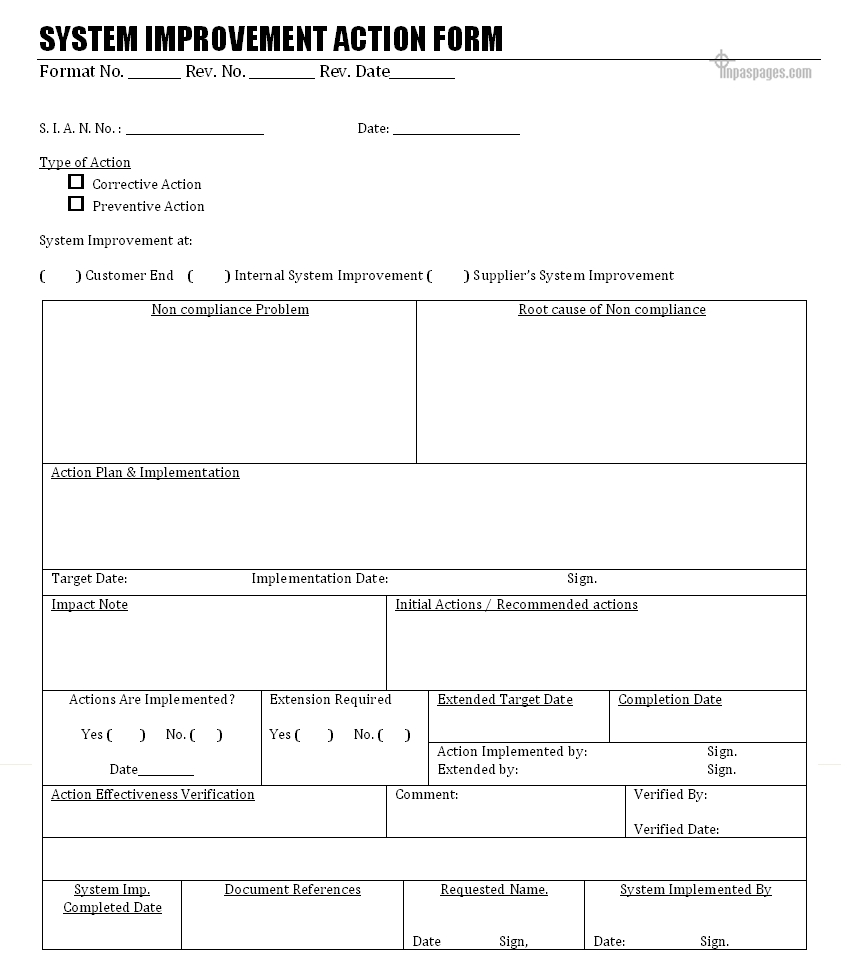
To implement quality system in company need to identify the non conformity of the system by auditing documentation, processes & sequences, all the found non compliance are need to comply in time manner to maintain system. Non compliance are the leakage of the system procedures, when any process or part, activity is not met to requirements of the system standards that are non compliance. All the non conformity are finds are results of audits in internal quality audit, during the audit all the non conformity are conducted and recorded for the fulfillment. Internal Auditee team is conducted all the non conformity for the identify root causes to eliminate non-conformity to ensure the product quality and quality management system.
On base of the root cause and identified causes, corrective actions are taken, corrective actions taken to eliminate the causes of the nonconformity, defect or situation in order to prevent repetition of the issue, same the preventive action taken to eliminate potential repetition of non conformity or defects in the system or product. Corrective action might be initiate due to result of customer complaints are raised reason of product quality concern, during the reviews of management or design review identified issues, manufacturing process or instructions issues, non conformity due to supplier or the non conformity identified by third party inspection or by customers.
Responsible personnel is conduct the implementation against non conformity are raised, all corrective actions are established on base of the process or issues and appropriate locations are identified and responsible for the non conformity. The implementation times are allow as per standard are defined and same for the customers and supplier’s implementation are conducted. Auditors are follow up in case the allow time for implementation is completion, and actions are noted for improvement, if the corrective action is effectively implemented the auditor team can reject the action and extend the time for the further implementation and actions. Now the Auditee team should complete the new action plan submit and implement accordingly before extended date completion.
——————————————————————-
Download system improvement action form
——————————————————————-