Preventive Actions for Prevent Potential Failures – This procedure describes how the potential nonconformity are identified and actions are taken to eliminate the cause of potential nonconformity in order to prevent their occurrence.
Stages of Procedures to prevent failures
The potential nonconformity that lead to decreased level of performance of processes and products are identified from
- The review of customer’s needs and expectation.
- Management of customer perception.
- Quality Records
- Past Mistakes and errors.
- Business development information.
- Data obtained during planning stage etc.
- Internal and external audit observation.
- QMS and procedure changes
- Preventive maintenance on tools and calibrations
- Opportunities for improvement(OFI)
- Process non conformity
- MOC if the preventive action affects QMS
- Quality Objectives
Step by step procedure
Reviews of Customers
The customer’s needs and expectation will come from a review of projects specification and discussion in the project kick -off meetings. The area of potential nonconformity is identify by taking into account the organization’s strengths and weakness.
Measurements of customer perception
The measurement of the customer perception in the early stage of the project and the level of organizations expect level of performance will bring out areas of potential non-conformity which can lead to low customer satisfaction.
Quality Records
The quality records and the experience from past performance are use to identify potential nonconformity on the projects. Evaluation of the needs of a preventive action and any short term actions require to prevent occurrence of a non-conformity.
Market information
The market information available with the top management is also use to identify potential non-conformance.
Internal & External Audit
The observations that are brought out in external and internal audits must also be use to identify potential non-conformance.
Potential N.C.
The potential nonconformity can be identify by any personnel in their processes or in other processes report to QA Manager. On receipt of information or on identification of the potential nonconformity, the QA Manager records the potential nonconformity and distributes for future action.
Investigation
The investigation for the reason of the possible non conformity is carry out by the QA Manager or the department manager responsible by interacting with the personnel involve.
Potential N.C.
Once the reason is determine, the possible methods to eliminate the cause for potential non conformity are work out. The right method is choose from the possible method by the process owners in consultation. The QA Manager and records in Preventive action form.
Implementation
The select preventive action is close and implement within 30 days from initiation of the PAR. The results of the implementation should be monitor. A follow up is made by checking whether the expect potential nonconformity is likely to occur or not.
Prevention from re-occurrence
If the potential nonconformity has been prevent from occurrence. The results must be review, and the steps from section above must be follow.
Expecting Results
If the preventive action are takes and even not provide the expect results, then the method should chose to eliminate the cause. Even and must be review, and the steps from section above must be follow.
Preventive actions process
The preventative action procedure can also be apply in the support processes like information technology Maintenance etc.
Preventive Action Tracking template
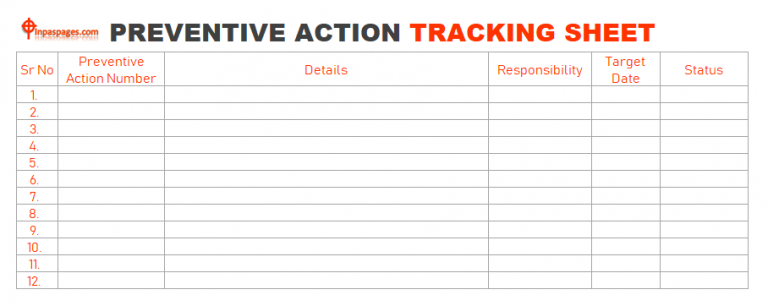