Obsolete or excess inventory Disposition
Excess inventory disposition is part of the system procedure to manage various functions involved in handing and disposition of obsolete or excess material.
Obsolete or excess inventory disposition is the method or system that helps to handling and disposition of excess material which is not used or not for used in production or manufacturing activities. Excess inventory is generated from many ways:
- Product failure during the producing material in manufacturing processes.
- Samples are taken during the in-process inspection conducted by quality department.
- Whole lot or batch rejected during the inspection or at the final stage material rejection is one of the important reasons.
- Material which is generated as the waste during the various manufacturing processes is also conducted as obsolete inventory that not excess inventory but its not useful for the further processes and for final product.
- When the material is not met the customer requirements, technical specification or any other customer end application issues due to supplied material rejected by customer that are also count in excess inventory.
- But the important excess inventory is the material which buy as raw material from the supplier and the material is in stock from long time but not in used that mostly count in excess inventory and this is very critical inventory and situation that company should take the serious actions for manage it.
The obsolete inventory disposition is part of manufacturing and other concern system that all the employees are responsible to maintain system in the company, the system helps to identify, tracking and proper arrangement for excess / obsolete inventory in manufacturing procedure. The excess inventory disposition relate with from raw material to final inspection. All the excess inventory /obsolete inventory is conducted by proper recording the information to send to excess inventory storage, the format for the conducting the material at the excess inventory storage according the excess / obsolete inventory form with proper required details should conducted in format. See picture below is given for reference:
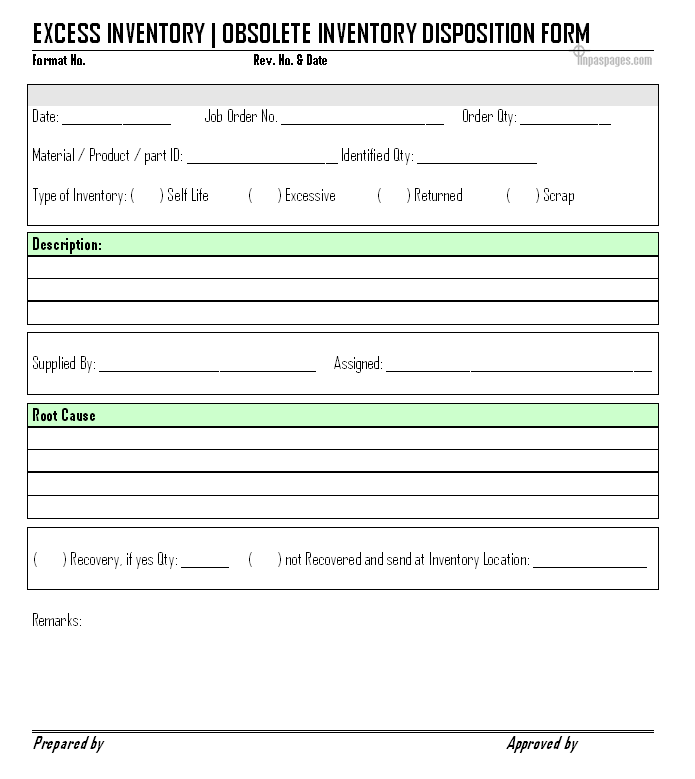
Excess inventory material is generating from various manufacturing processes, raw material handling, storage and movement, material which is not in used by the product specifications or any other issues the customer demand can also reflecting the excess inventory. For the controlling over the excess inventory need to fully controlled over the system and procedures strong follow up, some industries are used inventory turn over ratio system that helps to reduction in excess inventory in the stocks.
Obsolete / Excess inventory and cost effects
- Raw Material – Raw material stocks and procurement is major cause of the excess inventory, raw material procurement system is not proper handled or calculations are not very effective making balance between internal manufacturing process and customer requirements with possible minimum stock which indicate re-order level. Raw material procurement is prime responsible that managing the raw material as per requirements of the planning and customer end, planning team is sending its plan / schedule of future requirement of customer along with current in process orders, management team is considering the values, market stabilities and other factors for the raw material procurement, management think that material requirements cost in case low in the period that extra material is procure which can cause excess inventory, but in long term its direct loss for the management. All the procure material should be proper calculated, customer trend of requirements, current situation of the market, current cost on manufacturing activities, and possible excess inventory generate should consider before the procure raw material, if the directly to see the market cost is not correct way for purchase material is became excess inventory.
- Shelf life – All the incoming raw material has a shelf life, an concern peoples should determine the shelf life and all the concern information should proper record to tacking in processes in manufacturing activities, shelf life information is very important for the materials like foods, chemicals or similar material that appropriate material’s tag / stickers or label are need to peoples get the idea to handing the material and sending the material by the systematic ways like FIFO system ( First in first out ) to maintain system and used material before its self life is expired. The status of such material shall be checked periodically to each stock on the frequency defined by management or requirements of the material to inspected. On expiry of the material will be considered as obsolete material and separate inventory is maintained in this regard.
Control for Excess inventory / obsolete inventory
There are many ways to controlling the excess inventory in the manufacturing unit, when the raw material procurements are purchasing the raw material, its should need to proper calculate the requirements, situation, customer market trend and future possible requirements of the customers, if the management AS AND WHEN REQUIRED system is apply that possible to conduct the maintain inventory, as and when required is not meaning required stock is not maintain, all the sides of coin should be consider that possible to control on excess inventory stock, there best example is conducting the system “Inventory Turnover Ratio”, Lean management, 5S system, MFCA system helps to manage it.
Conclusion
Excessive material / obsolete inventory is material / product that has not been used in a long time period and can not be used on current product or manufacturing process due to shelf life, not ordered from customers or any market trend change or any other reasons. All excessive material has been determined to proper stock and immediate consumed. All the excess inventory or obsolete material inventory is reviewed by management team and appropriate actions taken on it on time period / frequency of review defined by management. All the excess inventory / obsolete inventory is segregated and separate storage to individual actions are possible and on base of the root cause analysis all the material excess inventory are inspected, in case the material is possible to recover for the further used that corrective actions are taken.
———————————————————————–
Download format in Word document | Excel Sheet | PDF format
Download Excess inventory / Obsolete inventory disposition form
———————————————————————–