How to effectively implement Kaizen for material movement
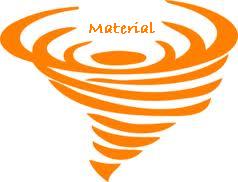
Overview to Kaizen Material Movement
To proof best practice to improve productivity of manpower as well as machine, Kaizen can enhance reduction of human motion & tracking orders or lot to reduce time in between of production line steps by reason of machine trouble or other Applicable cause.
Material movement inside the production stages are much important to move on base of planned to achieve target in bounded time, that is timeline can be reduce if material not to be hold in between to machines or any location / area or on equipment that is only count in waste of time & money.
Kaizen Material Movement – Monitoring
To avoid the losses that need to tracking, monitoring, controls & training to workmen & maintenance for data analysis to realize to people to whom concern for past holds of materials are responsible & why it’s happen to not move material.
Enhancement of material movement tracking can also use good technical manual systems, new ideas with group discussions or intelligent computer system, now days in market there are too many advance lot / material / order tracking software are available with low cost that can be affordable financially but need to handle properly. Any method is acceptable to rightly tracking, monitoring on material movement are on way as scheduled.
Data Analysis – Kaizen Material Movement
On base of data analysis of material movement tracking / monitoring that found any reason to hold that can need to identify immediately by root cause of trouble of machine or any others. Its very important for lean cost of material final cost can reflect, only data analysis / recording of trouble is not enough, need to shoot out the problem as root cause founded on report.
Main factor to enhance costing of material that is only waste in production line is
- Material hold due to breakdown of machine
- Due to humans’ awareness or other reasons.
- SOP insufficient / Training gap
Major factors are mentioned above can mostly found on base of any cause that tries to avoid on begging of any jobs / new developments / project.
Second step for material movement tracking – Make Material / Lot / Order tacking sheet.
=====================================================
You Might Also Like:
Kaizen: