APQP definition
Advanced product quality planning
Advance product quality planning documents managed to development of new products to ensure the developed product quality.
Overview
The applicability to all manufacturing products / manufacturing processes development concern activities and its documentations as well as all the modifications, amendment, records in the manufacturing facility, for the existing products and manufacturing processes supporting activities changes in the product specifications, standards, characteristics requirements, raw materials, bill of the materials, or product’s current manufacturing scope and range are considered in the new product development that basics are directly affecting in the procedures is managed and covered accordingly.
General requirements and inputs
General inputs for the new product development, advance product quality planning is main sources is customers, the customer product requirements is considered on the prime / pivot inputs to conducted the APQP and new product development process. Hence the manufacturing possibility, feasibility as internal capacity and stability of the product manufacturing, history of manufacturing that is previous product and process development experience and similar product / application products for the manufacturing is considered.
Develop system practice
Process cycle
The system practice is manage on activity of advance product quality planning. It may is conduct for any customer specific requirements, technical and characteristic requirements. When the organization receive inputs from customers for its end applications. The manufacturing processes, product and machine parameters should be conduct for verification and setup. As well the manufacturing process cycle needs to establish according to advance product quality planning on as other hand. The requirements of the conducting the APQP activities needs to managed APQP time schedule.
Inputs from customers
The inputs from the customers on after receiving inquiry for the particular product for development. Where needs to manage new product, that immediate actions are need to discussion on initial feedback. The ways to compliance of requirements are can be manage cross functional team. They will manage the all fields requirements and its considerable values as scope of customer expectations. The documents supporting as the inputs of new product development is customer inquiry and enquiry review form.
Process flow chart & Planning
The team is conducting the initial planning & determine / define action plan or program that use to follows outputs requirements. They will generating records of customer specific requirements to specific to product performance. Team may manage the require flow of processes to manage process flow chart and process diagram for manage the product for the manufacturing accordingly. The team should be managing preliminary listing of each special product and process characteristics as customer inquiry and technical requirements. Hence the all initial risk evaluation should be considered during the planning. To ensure that possible risk and its considerations.
Product Design & Development
The product design and development teams are consider possible outputs to manage customer provided drawings and specifications. That may needs to conduct for reviews to determine results as finalize the product drawing and specifications. Each special characteristics are require to consider during finalize drawing and specifications. The team should implement controls plan as needs if as prototype, should develop if customer needs. The process design teams is manage the standards requirements for the packaging, shipping requirements as per product standards and customer needs.
Product quality requirements
The quality requirements are manage by quality or cross function team to conducting all the existing processes and products to verify the process flow charts. New product requirements to identify different for existing processes and product that easier for manage ground requirements. Planning at the manufacturing processes levels at the floor.
Process FMEA
The important tasks during the implementation of new product development needs to establishment of process / product failure mode effective analysis (PFMEA). To instructive documents for new processes in case needs to develop that helps to care of development processes and process capability study.
Product | Process validation
The team is conducting the product and process reviews and validations to ensure that the developed product and processes will be maintain quality of product. As well requirements of end application as customer expecting. Hence the inputs from the design and development team are conduct to verification and reviews accordingly.
The team is conducting analysis that is measurement system and its evaluation where initial process capability study is cover. The team should be verify the sampling plan and production part approval process should be maintain to acknowledgement and approvals from customers.
As on submitting the records and samples to customers, all the feedback are conduct as inputs. Its assessment are manage as corrective actions, and implementation to reduce various / deviation in the product as per sample submitted. The process controls are manage by special techniques and process controls requirements to stabilize processes as applicable requirements of customers.
APQP & Customer Satisfaction
The APQP (Advance product quality planning) for the new product / process development is key tool that need to manage. Its proper reviews should be maintain to define frequency, generally the reviews are conduct in the management reviews meeting. So the whole process is manage for customer satisfactions and end application requirements.
The processes & product development should be comply all the requirements. The documentation for the APQP are managed accordingly to requirements. See picture below given example format of APQP time schedule helps to manage records and provide for education purpose:
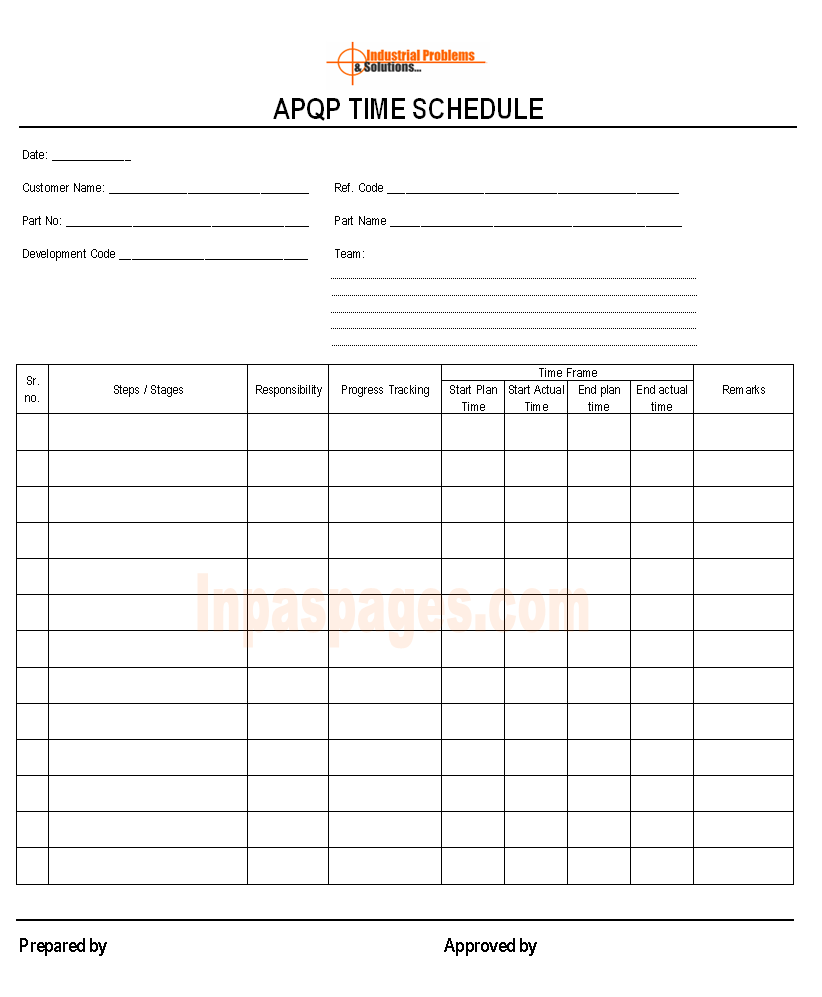
————————————————————————-
Download format in word document | Excel Sheet | PDF format
APQP time schedule
————————————————————————-