Job safety analysis and instructions
To ensure that job safety system is operating effectively by job analysis. The system is used to identify & control the existing hazards for each job performed in the working environment.
The process establish & improvement in floor level is responsibility of management representative of safety, but its all the concern peoples contribution is very important to identifications, follow up system and controlling over hazards in the existing jobs.
Job safety analysis is identifying the hazards in regular working job process by activities monitoring for controlling by instructions & changes. Working environment is clean, safe and secure for all employees are always expecting by management but the working environment how to make is very important and immediate actions on the changes in process, modifications in the equipment are very important but its all are done after the working environment analysis. Company are working with many manufacturing processes that all are not same or similar, some processes are very having risk during the operating which needs to identify, monitoring and control is very important for the makes safe and secure working environment.
The Job hazard analysis system is apply to all the existing jobs to identify, monitoring and controlling on hazards activities, process and equipment which are used in process support or part of process, procedure for identification of hazards & control measures.
Identify hazards in jobs
Manufacturing process are working with heavy machinery, equipment, hazardous chemicals and chemical reagent which can directly or indirectly harm to human body & environment, identification of the hazards in the regular & new jobs is very important by the analysis of the each stages, bill of materials, activities and used supporting materials. Generally management representative or safety team are interacting with process owners and operating peoples that regularly working on processes are explain better for the possible hazards, management team is all the identified hazards are defined in categories for the proper controls.
Identification of hazards / aspect in job are conducted to listing the all current jobs and for new jobs, In the particular job how many processes / system are needs and for the run process in manufacturing activities what is the requirements are conducted for the analysis, all the process wise requirements are collect and analysis are establish for identifications of hazards, for each hazard safety instructions or management is providing the safe condition to control over it. Here as below see example of job safety analysis and instruction sheet in picture:
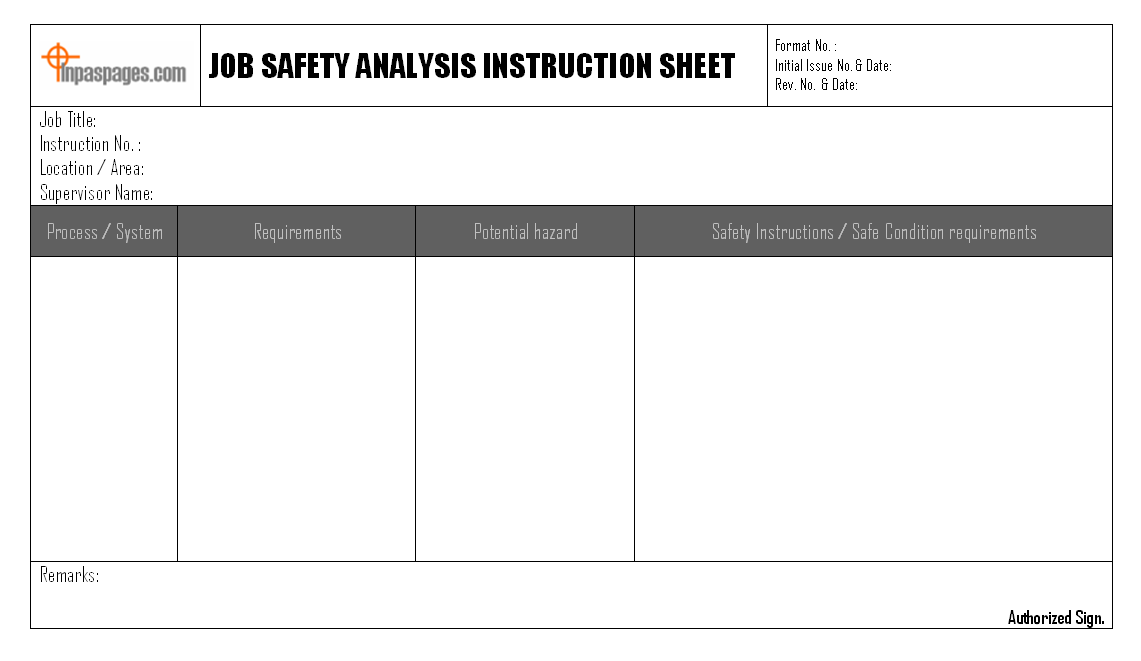
Job safety analysis is a method for analyzing job conditions to identify hazards and the potential for accidents associated with each process stages, by the development of the proper controls that helps to eliminate or minimize risk level for prevent accidents. Job safety analysis must include all the process stages & sequences of processes to possible suggested actions or particular procedure to control these potential hazards in existing jobs.
Job Task hazard review
Identification the active process in manufacturing should be developed inclusive record of the jobs & task to maintain each job task stages, activities and sub activities. On base of the process requirements, hazard exposure frequency, risk level, type of risk / hazard is consider to manage controls on the risk and potential hazards to evaluate hazards for individual jobs. Risk evaluation and its level are defined on the possibilities and severity caused by hazards in jobs, each high potential hazards are listed that should immediate eliminate or minimize level of risk by deployment of controls.
Risk control
To identify priority of requirements to controls on hazards in job safety by analysis and the risk controls based on the job risk assessment results, appropriate control measurements needs to defined to eliminate or minimize risk level. There some actions there taken to decided after the assessment and find out the possibilities of the controls over it, If the possibilities of the elimination of the potential hazards which can be process, equipment, system or anything which possible to completely remove form the system, if the possibilities or the substitution mean involves using non dangerous process, system or equipment to replace the part of the conditions, by the engineering changes possible to controls over the potential hazards its can be minimize or eliminate its all depends on the hazard and concern process if the not possible to completely remove from system, management try to minimize level or risk.
Job Safety Analysis Process
Job safety analysis should conducted for the each job allocated for the manufacturing process in working area, all the records are maintained in the job safety analysis record formats which is timely updated for the collecting the information for the analysis. By job safety analysis management decide the action plans to makes the safe operation process concern jobs. Potential chemical hazards, supporting tools hazards and supporting equipment like crane, lifts, chemical leakage, sewage, oil, gas etc, causes hazards in the working environment, so proper handling, operations, maintenance, work instructions, M.S.D.S. awareness, Personal protective equipment are options to control over it. Safety team is considering the previous year records of the injury and illness, accidents, near miss in the working areas for the get the solutions to eliminate or possible controls on it.
———————————————————————-
Job Safety analysis instruction sheet download[word]
———————————————————————-