ISO 9001 purchase audit checklist is systematic document use to ensure the all purchase goods are maintaining quality standards. It may use to inspect all incoming raw materials & consumable goods that may directly affect the manufacturing processes & final product.
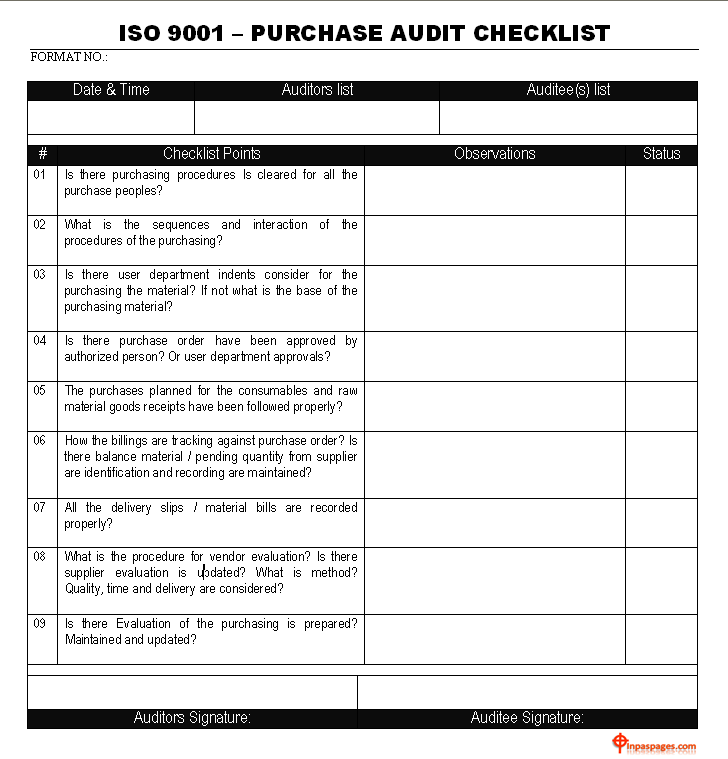
Overview to Purchase audit checklist
The purpose of the purchase audit to ensure that all purchased products confirms to specified requirements.
The purchase audit checklist may use to inspecting a all incoming purchase materials. It may verify the compliance of quality standards, general quality, and internal requirements. The checklist can help to reviews overall purchase system and its documentation.As standard practice, I can manage purchased products in following categories:
- Raw materials
- Consumable goods
- Finished products
- Su-contractors / third party services
The management needs to defined proper controls required to ensure that product conform are the same for all above categories.
General requirements:
- On of the important aspect of the quality management system is approvals of the vendors. each vendor which are actively supplying materials should be completes the quality system requirements. Even, the purchase team must update the vendor approval list regularly. Vendors are specified for and moved from the approved list on the basis of overall vendor rating.
- Identification of raw material requirements and stores, general material requirements should have complied.
- Generally, it may be standard practice of the purchase team to prepare purchase order with all relevant information. Even, purchase authority may also require to verify the each purchase order, review, sign and issue accordingly. Further, each purchase order may have to include all the technical and commercial details as per product ordering.
- Take care during the selection of sub-contractors. Check the previous performance of each sub-contractor, select those contractors are providing a satisfactory services yet.
Some required vendor registration and rating:
- Registration of new vendors
- Evaluation of vendors
- Gradation of vendors as per adopted criteria
Audit for verification of purchased product: requirements
- All the incoming raw materials / consumables / chemicals and other stores materials i.e. all purchased materials received are inputs in the documents.
- It is on of the important part of the store management. Each materials are receiving should be properly identify, and define a categories for the segregation process. it is also good practice to store each materials as per its category, stack, and mange separately.
- The quality requirements i.e. dimensions, quantity, specification and technical requirements should be verify and enter in documentation or in system.
- All the purchase materials should be tests and its test certificate with order specification are receiving, in case of loose, local purchase materials should be proper inspect.
- Incoming materials needs to internal tests, verification, inspection is necessary in the ISO 9001 guidelines and system requirements hence all the analysis receive from define testing laboratory is records in inspection documentation.
- Audit team verify all the transfer / issue materials in the production lines should be properly test and inspect by qualify inspector.
- All non-confirming materials is segregate and manage / storage separately with appropriate define location with status tag and marking.
General checklist points:
- Is there purchasing procedures Is cleared for all the purchase peoples?
- What is the sequences and interaction of the procedures of the purchasing?
- Is there user department indents consider for the purchasing the material? If not what is the base of the purchasing material?
- Is there purchase order have been approve by authorize person? Or user department’s approvals?
- The purchases plan for the consumables and raw material goods receipts have been follow properly?
- How the billings are tracking against purchase order? Is there balance material / pending quantity from supplier are identification and recording are maintain?
- All the delivery slips / material bills are record properly?
- What is the procedure for vendor evaluation? Is there supplier evaluation is update? What is method? Quality, time and delivery are consider?
- Is there Evaluation of the purchasing is prepare? Maintain and update?
Audit review
Products, specifications, technical and other commercial details should be identify and clearly mention in document. All the technical documentation define as product requirements / and end application requirements like standards, specification, drawings, sketch and expectation of end users. All the require quality records like testing, inspection and its test certificates, warranty and guarantee details. Same the details should be mention in purchase order.
EXAMPLES, SAMPLES & FORMATS: Download
Related: