Dispatch Clearance Process and reporting
Dispatch clearance process is guidelines to clearing material from quality to managing requirements of packaging, labeling and marking on product for deliver to customer.
Dispatch clearance process introducing requirements on after product passed from final quality stages, quality should follow the dispatch clearance process part as the clearing material for the further actions, quality will move the material to concern department which is labeling on the product, marking on product and packing according to standards of packaging requirements.
The process is conducted to clearing material from final stage of quality to deliver the material to customer, when the material became approves by the quality department, material should be immediate clear from the quality for further process, the system is push the material to move the at other departments, reason that generally we shown the after the quality inspection on the final stage, material is move when the management instructions, unknown about material finalization, appropriate guidelines for materials or any other reason the material stay after quality passed, but management needs a system i.e. dispatch clearance process which not need to further actions or separate actions to clearing the material from quality department, the process of quality at the final stage should required system to automatic material move.
Dispatch clearing is the responsibility of the quality manager whenever the material is quality passed, and as and when material reach to packaging department that responsibilities are transfer to dispatch and packaging department to immediate clear material for dispatch process, the assignment of responsibilities are concern to material movements, requirements of processes and sequences of the company. The procedure helps to managing the activities of the quality, packaging and dispatch processes.
Dispatch clearance process is introducing strong system to process encourage to move material for the next station, cleaning of the material at the quality department are conducted on after the final stage of the material, documentations is helps to managing the dispatch clearance process, in the quality department, whenever the material is completed all the quality process, quality department should be submitted the report to management as well as packing department, and at the time dispatch clearance report should must to submitted along with material, without the dispatch clearance report, packing and dispatch will not received the material as well as documents, hence packaging department should be submit report along with the dispatch advice with dispatch clearance, see picture below for the dispatch clearance report:
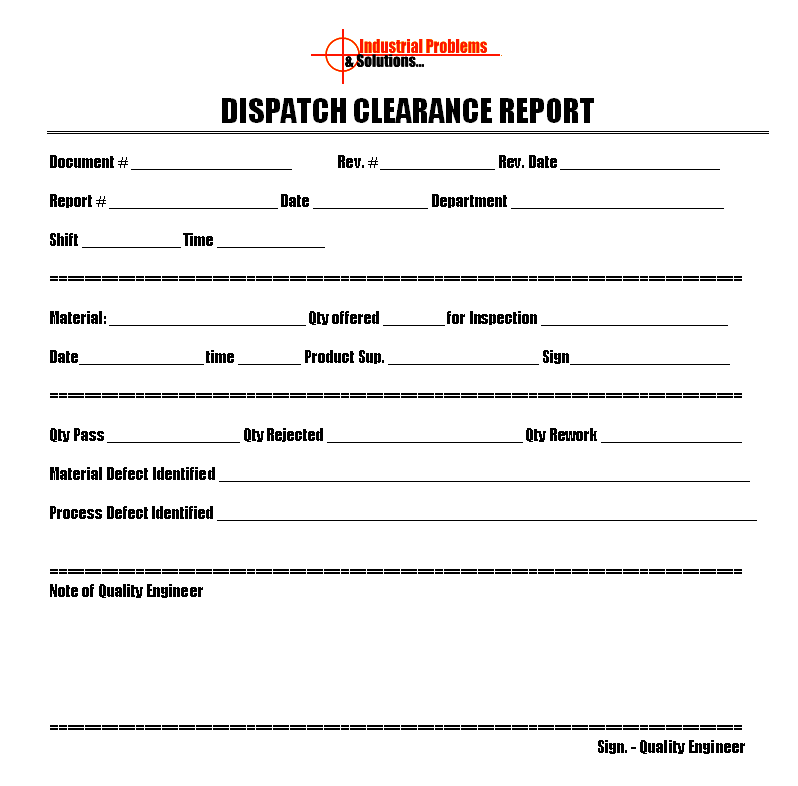
The dispatch clearance report is prepared by quality engineer, behalf of quality department to describe the material conditions. In dispatch clearance report generally material details are included along with the quantity offered to next process, or for the next inspection, there are also included dates and time with name of the person whose will conduct the next process. In the dispatch clearance report is included material which is passed by the quality department in quantity specified by the transitions, in case the material is rejected or rework are need to conduct for the same works are mentioned in the dispatch clearance report. Material defects identification information or if process defects are defined during the inspection process are also need to mentioned in the report, and finally quality engineer is mentioned short describe of the whole process and sign and stamped, quality department send the material along with dispatch clearance report to packaging or dispatch department for the complete further formalities for the deliver the material to customer.
——————————————————————–
Download format in Word Document | Excel Sheet | PDF format
Download dispatch clearance report
——————————————————————–