CAPA & non-conformity :
The processes describe relation between corrective actions & preventive actions (CAPA) with non-conformity (NC) for stability of quality management system.
The purpose of establish and maintain a process for corrective actions is to reducing / eliminating the source causes of non-conformity in order to prevent recurrence. Hence the preventive actions process is established to eliminating the cause of potential non-conformity’s to prevent occurrence.
The both processes are helps to continually improvement to performance of processes concern quality management system. The processes defined that is corrective & preventive actions measures in the various processes, workplaces and locations in line with requirements.
The corrective actions & preventive actions both are conducted for elimination of non-conformity in sequence of implementation requirements, hence the top management is activity participate in the actions to aware the concern personal for implement the task with conformity.
What steps can prevent non-conformity?
For the effective implementation of quality management system in organization needs to prevent non-conformity to follow up quality system requirements, procedures, guidelines and instructed by system and training and awareness to all related employees should be provided, and assigned responsibilities and authority for their concern job. Some basic steps that help to preventive non-conformity are as below:
- Ensures that the quality management system defined procedures, guidelines, instructions and documentation are strictly followed and has been implemented.
- The employee should be support to the corrective action request process and worthwhile initiative as and when required.
- All the corrective action request process should properly manage controlled and related corrective action requests should short out within the agreed time scale, and to ensure the implementation, monitoring of solutions.
- CAR (The corrective action request is document use, as tool for managing and controls on non-conformance)
- The management representative should be actively participate and monitor on activities of concern of the corrective action request processes, the follow up of all corrective actions request’s ensuring completeness, and analysis and update the status of each request raised and discuss in management review meeting.
In the organization, general sources which are factors that could initiate corrective actions and preventive actions are:
- Non-conformance with existing deployed internal management system, standards
- Changes to governmental, environment, health & safety requirements.
- Internal audit / external audit resulting identified non-conformity reported about internal system.
- Customer complaints
- Personnel, departmental, organizational unsatisfactory performance level measurements identified.
- Maintenance requirements of equipment, machinery, service breakdown occurrence.
- Identified high costs unnecessary.
- Identified possibilities of improvement in locations, areas with existing processes.
The document every non-conformance are require to register, and document in specific reports. See picture below example for education purpose:
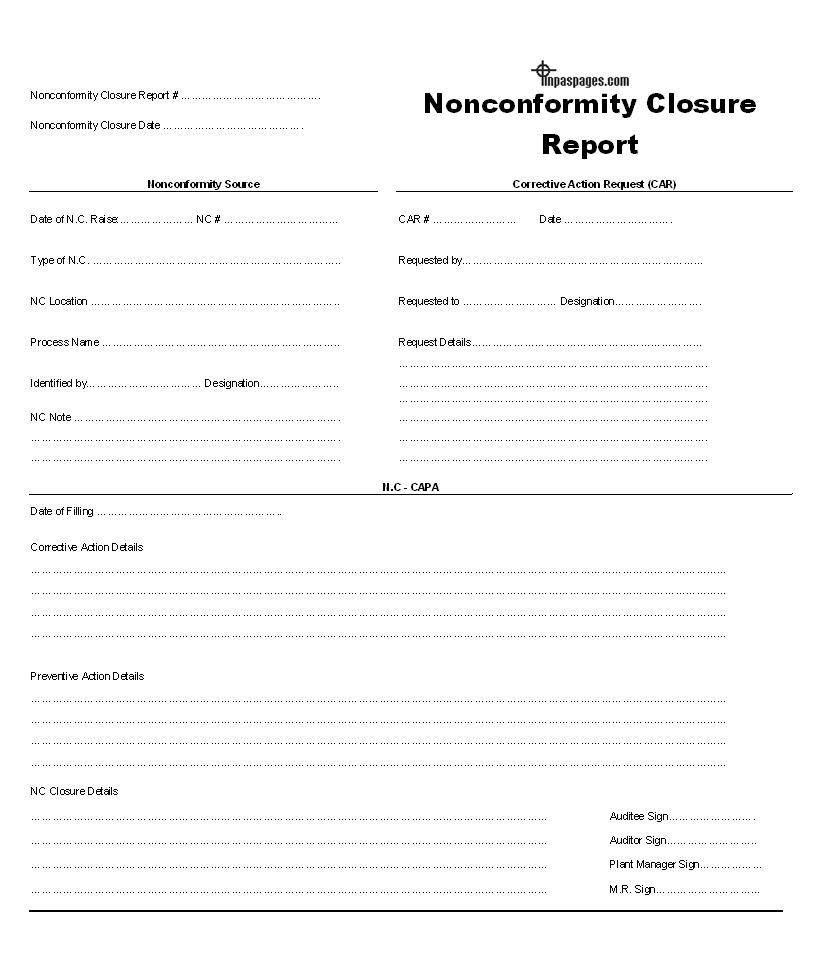
————————————————————————————
Download format in word document | Excel Sheet | PDF format