CAPA form – Corrective action and preventive action
CAPA Stand for Corrective Action and Preventive Action
Why CAPA?
To ensure that preventive actions are taken to reduce potential non-conformance, corrective actions are taken to eliminate root causes thereby cultivating the performance of quality management system i.e. internal management system.
How to apply in process?
This method or process apply where actions needs to controls, reduce or eliminate potential non-conformance which are raised in manufacturing processes, activities or any materials. That can be includes:
- Product or services
- Manufacturing processes, process deviations, hazards
- Customer related issues
- Leagal non-conformances
- Internal management system and documentation related.
Process description table / Chart
Primary responsibility | Overall Responsibility | process objectives | Inputs | Outputs | Method |
---|---|---|---|---|---|
Generally, Management representative and head of department | To implement a procedure to identify and eliminate actual or potential causes of non-conformities related to product, process and quality management system. | Numbers of complaints, materials Rejection minimization, Numbers of CAPA | (1) Product(2) Manufacturing Processes (3) System / Internal – Non conformities | Current status of CAPA and its action | (1) Contiunal Improvement Table / Matrix (2) KPIs, Quality objectives, Process perfomrance indicators (3)Procedure ensures continual improvement |
Identify CAPA requirement
- Corrective & Preventive action should be conducted for all incoming that is raw material rejection, in manufacturing process non-conformance, in-process rejections it became rework, customer complaints and related issues. All incoming material quality, and its documentation should be properly handled along with details of records, non conformance analysis report should be prepared and must submitted to concern peoples for further action, concern department will be identify issue and make the CAPA form for identify root cause and eliminate issue with perform the preventive actions at appropriate location.
- All the customer complaints should be in written format, and action initiated as related procedures for customer complaint handling, further all the customer complaints should must review in general meeting, and all the actions i.e. capa reporting and same issues at appropriate locations should mentioned in it, so the concern peoples can understand the issues and occurrence at machinery or location.
- All the corrective actions and preventive actions should be collected, reviews and implemented output points from general meeting, in case of any pending corrective and preventive action should reviewed at defined frequency in internal management system.
CAPA Form
Actions that taken for the correction in line with non-conformity raised & same preventive actions are taken to other same issues or department that eliminate possibility of the issues.
CAPA form is filling up when expecting for improvements, preventive action or compliance of the non-conformity, generally below points are need to comply in CAPA form:
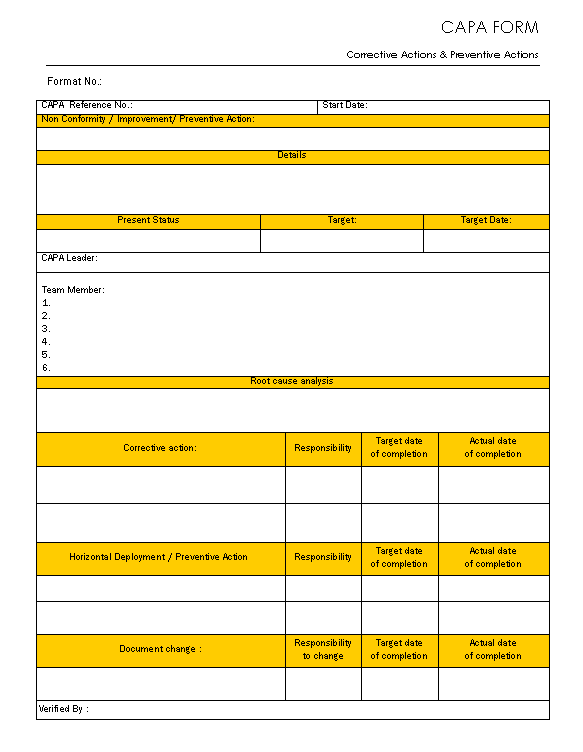
- Details of the non-conformity raised or improvements points that can be process improvement, product improvement or compliance of the non-conformity that detailed information are easier to focus on the subject are going in pivot.
- Present statuses of the subject are also need in CAPA form against target information and target time frame also needs to focus on goal.
- Any project needs the lead person that CAPA is also well project that leader information and same will be team members’ information also incorporate.
- On base of the information CAPA team are find out the causes that oppose the progress or reasons of the non-conformity that is root cause of the problems or troubles, if the root cause is systematically in state direction that project success hope in increase and solutions are also comes on light at steps are goes on path.
- Corrective actions on the problems / subjects that disturb the progress are correct for the subject taken on next higher level.
- Preventive actions – if the same troubles / problems or opportunity of improvements are found in line with corrective actions that takes on places for the improvement those department / product / process or subjects as preventively takes on hand for the improvement before the problem raised that eliminate possibilities of the problems or advance improvement.
- Due to changes in the process or products or any instructions that documents change can be possible required for the modifications / update or upgrades.
All above points are part of the CAPA form format that help to business gone up, CAPA base requirements is mind storming, interact with peoples and right direction.
System Improvement
Corrective action and preventive action is also part of continuous improvement, the processes of capa maintain and improve the internal system to communicate each non conformance and perform task of actions accordingly. Generally, corrective and preventive actions are manage and improve quality management and increase customer satisfaction. See example below:

CAPA Analysis
Look the trend of the analysis data indicates that monthly / quarterly numbers of corrective actions and preventive actions are being down, that does not mean corrective actions / preventive actions are being lakes, but its indicates that problems are shoot out at appropriate locations, and occurrence and probabilities are reduced accordingly. At the end of the year, the effectiveness of the system improvement can be measurable and trend of effectiveness are possible to verify with previous years.