Operator training requirements for production lines
Operator training requirements are conducted to verification of each activity is conducted in production lines and identifies further training needs.
Operator training requirements and its processes are conducted to verification of the each production concern activities, machine operations and equipment handling requirements, and actual requirements that needs to maintain internal system of the production lines that identifier team is conducting all the activities in the manufacturing facilities to be maintained, and update information in case of the new technology and upgraded system is deployed in the manufacturing / production lines.
The system for the identification of the operator training, requirements and managing needs to maintain level of information and operating personnel, as changing or modification happen as below:
- When the manufacturing facilities are changed or modified any processes for proceeding materials.
- In case of the manufacturing facilities had change machinery / equipment or a device that needs to provide training to operator for the upgraded functions, operational manuals and other needs.
- If the management changed / upgrades system or deployed new system for documentations or system which helps to determine more sufficient environmental works in workplaces that operators should proper trained as requirements.
- Involvement in the safety, first aids and other safety requirements are needs to update.
- New join operators must be trained as all the company requirements, safety & manufacturing operation concern, generally in the manufacturing operations that are job descriptions, job safety guidelines, lock-out tag out general guidelines, training of the standard operating procedures and manuals, work instructions, documentations to maintain records of the operations, scrap and other waste managements, waster disposal etc..
As above some important points that help to determine individual new joint and existing operators are conducted and identified for the requirement of the training. The operator training requirements and documentation are prepared by concern managers and human resources department, concern managers are responsible for provides information of requirements, identification of the training needs as per departmental requirements and submit records to human resources department, human resources department is responsible for conducting those records and arrangement for the further needs of trainings. The records for the each activities concern training and it documentations are handled and maintained by human resources department for further analysis and managing other records to supporting system.
The training provider team is conducting the documents that provides by human resources department for the conducting data which are generated during the operator training and requirements that needs to managed and handled for further analysis. See picture below given for example format that is used for the recording information is production operator training requirements for education purpose:
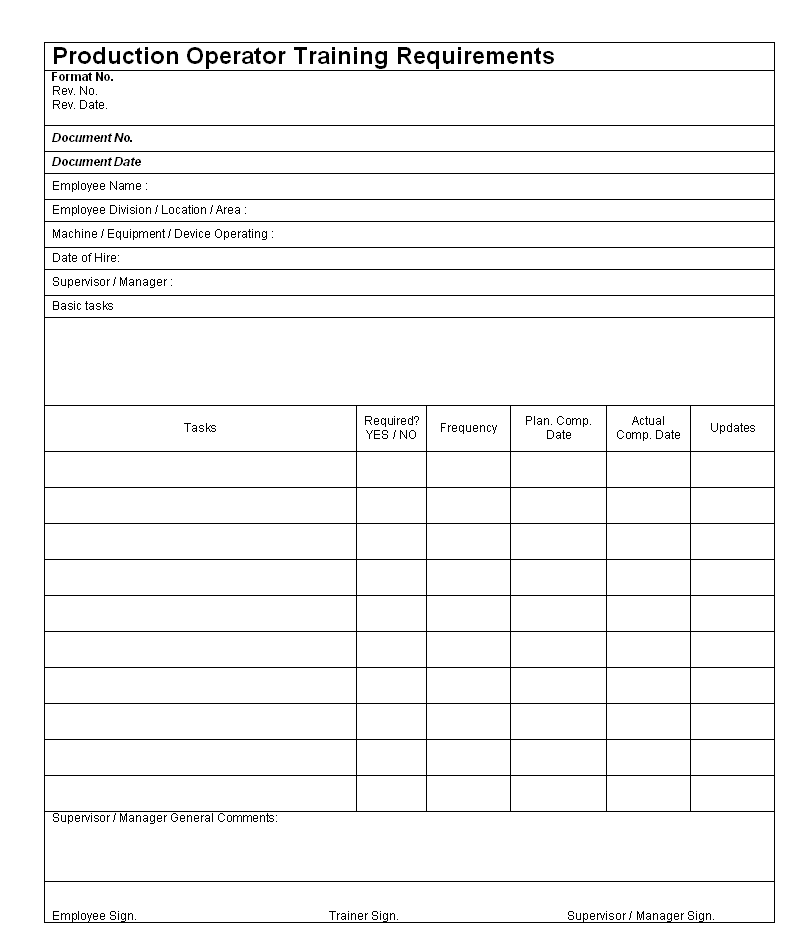
Production operator training records are maintained by human resources department, all the training concern records are maintained and update as per training are conducted during job period, production operator training requirements format and its document is maintained to provides the records and documents and same department managers are also conduct copies of records for managing operators as per experiences and qualifications.
——————————————————————–
Download format in word document | Excel Sheet | PDF format
Production operator training requirements
——————————————————————–
Related Posts: