Process analysis and realization
Process analysis is study of process parts (Inputs-operations-outputs) for achieve potential objective and analyze of process operations to determine actions for improve efficiency.
In any process having a major three stages where material is inputs as semi or raw material and at the end of process its became a finish material which is product, stages that interfaces between activities, functions and sequences that result of goal which is defined as process is established. There are major stages through realization are:
- Inputs – Material / Semi materials / bill of materials / consumable goods are general inputs along with documents that are plans, schedules supporting inputs for the process.
- Operations – All the inputs are conducted by operations thatare activities which dealing out the requirements of the ultimate results achieve.
- Out puts – the material which is inputs, operations are conducted and finalized the results as output from the process.
When the generally question is raised that’s about how any raw material / semi material will became final material or product that the information of sequence / interaction is provided by process analysis, the process analysis is describe step by step process parts’ information, operations, condition and explanation with detailed information to particular outcome.
The purpose of the process analysis is to explanation the sequences of stages are works by in order to manage and achievement of particular outcome. By the analysis company should not the whole picture of the process will get the results with the stage wise analysis, due to analysis the team determine the possible action to improvement in the process stages, amendment in the sequences for the effective and quality product. The material input in the process that became finish product is not just important for understanding; the product should be compliance all the technical requirements, specifications, customers’ requirements and end applications with the acceptable quality and defined criteria for the acceptance.
The team is conducting the process analysis on base of the management requirements, management change, process change or new product development generally, but in case the requirements are raised due to some non compliance are very difficult for the team, there are also possible to conducting the process analysis to minimize costing of stages of process or minimize waste level which is generated from the processes. Process analyzer are conducting the format for the process analysis which is called process analysis sheet to recording the information and managing all the parts required to understand and improvement if required. See below picture of process analysis sheet:
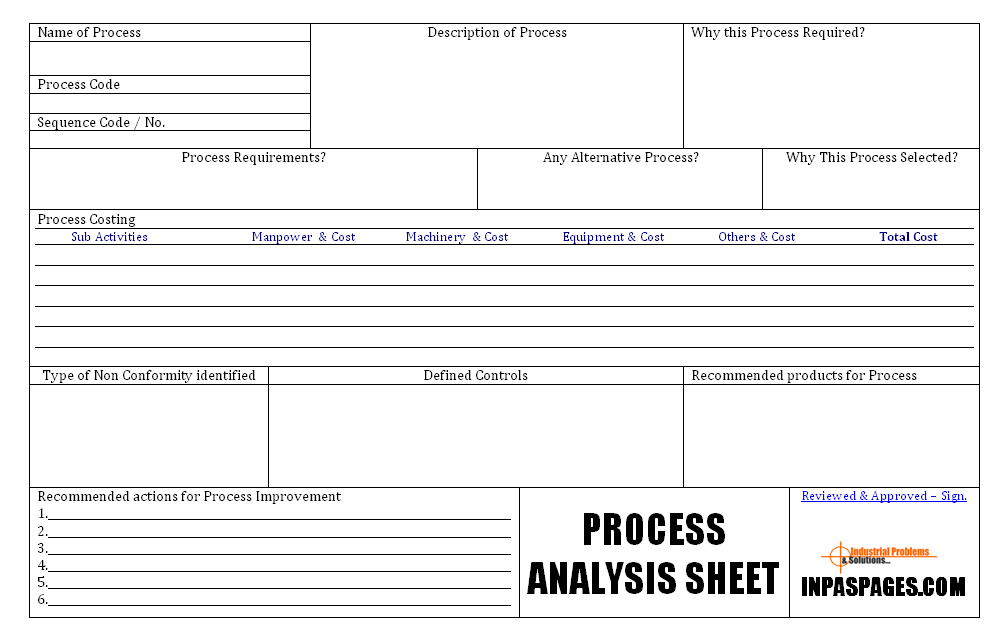
Process analysis is very tough job that possible to miss any part that the process analysis sheet helps to recording information in the sequence, operations and requirements of in process and supporting activities, whole process should conduct for the analysis carefully and ensure any step is not forgotten that the works are manage in process analysis sheet and this format made for it.
The most important part of the process analysis is “process Flow” on base of whole process analysis is conducted and before the process analysis should be necessary to ensure the process flow is addressing all the stages of the process, activities and sub activities. For improvement of process efficiency required to conduct subjective study, significant risk and level should identified for the controls and control measures are possible to deployed in the process.
———————————————————————-
Download Format in Word Document | Excel Sheet | PDF format
Download Process Analysis Sheet
———————————————————————-