Site Investigation
Definition
Site investigation is exploration of site to collecting information, identification of defects and analysis condition to determine actions for quality defects.
Purpose
Site investigation is conduct for the eliminate defects or identify solutions for the identified defects in product to visit the customer premises on customer complaints. This investigation is compliance standard requirements, customer satisfaction & quality product requirements, investigation process conducted at customer site to examine the product condition, understand when and why the product defect is identified, which process was running during the defects are identified some major questions are raised in site investigation and same are conducted during the site investigation to reach to source code of the product defect.
The company operates a system for dealing with complaints to concern of product quality upon customer feedbacks and complaints. Company is conducting the complaints and arranging visits after analysis of the product defects and concern peoples are visited to customer premises to investigate the concern issues of product to identify root causes and source of causes.
Quality Defect
A marketing team is collect the complaint from customer and forward to concern department, concern departments are communicate between each others to completion to the responsible managers for the product or process involved, and upon the complaints views or relevant errors, responsibilities are assigned for further investigation, investigation team is comply the requirements of the information, site investigation report is raised and along with investigation, site investigation report is filled along with. See below picture for the site investigation report is filled by concern department for the further information:
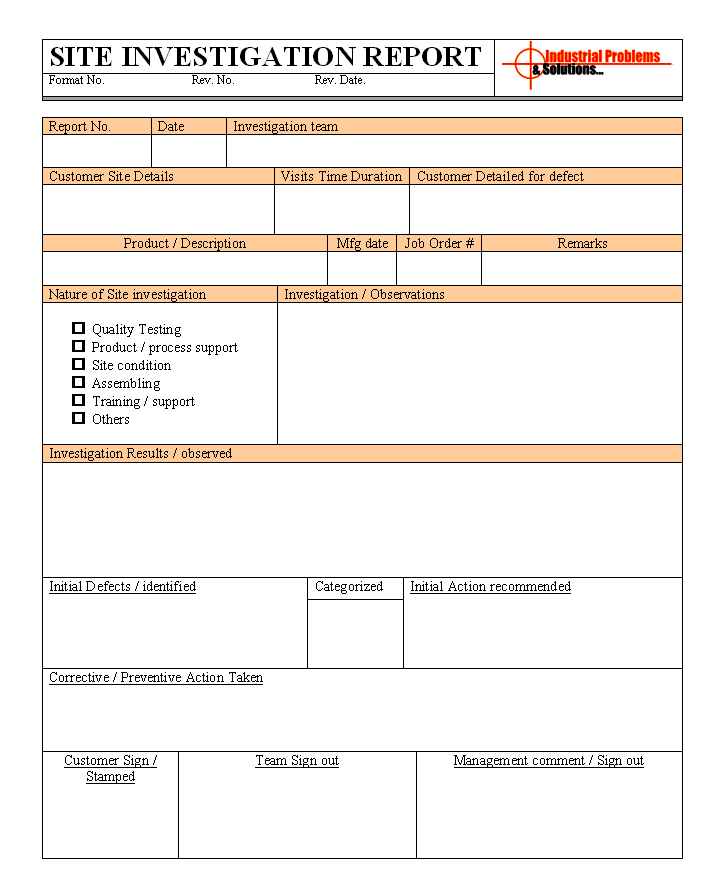
In the part of the site investigation and objective is the identification of quality defects in the product which is located at the customer end, mostly in the engineering, heavy machinery, automotive applications internal parts suppliers should must visit the customer’s end to identification of the product defects, observations on the customer’s processes to know the facts of the products used & find out solutions in bound of standards requirements of end applications.
Quality defect investigation report is required according to quality standards and during the visit investigation team is identify the quality defects and same for the initiate an investigation to establish for the identify root cause of the defects, on base of the quality defects identifications classification of quality defects are taken impotency to manage the controls over it.
Critical defects considered which are potential risk for the end applications, wrong product or different standard / grade products, wrong contents is considered as critical defect. Product that supplied correct but the product sizes, material strengths, and mechanical properties are wrong is considered as critical defect. Critical defects categories are identified as the product which is useless or making a serious risk to end application which is not possible to eliminate after installations or end application’s requirements is not fulfilled are considered as serious defects or critical defects.
Minor defects are considered which the product are supplied to customer having the mislabeling, incorrect information are passed along with the product, excess tolerances in the products, part of the product is mixed with another product, stabilities in the specifications are mismatched. Generally faulty packaging, wrong closures are reasons of the defects that consequences are raised to customers end.
Conducting Investigation
The investigation is conduct to establish root causes of the quality defects, responsible technical department is conducting investigation part of the visits to manage critical defects of the product, but the first of all ensure the defects are not be local or customer end’s process, investigation team are check and complete induction processes as requirement of investigation procedure. Investigation team conduct investigation on base of initial investigation that localized damage, product cracking, material difficulties, site conditions by visual inspections and by the testing of the product as per standards to ensure the product fulfilled with standard requirement or not.
Investigation team should considering the information from the material inputs at the customer end, temporary storage, handling for the processes and in process sampling details are conduct and analysis to root causes, the fact finding are conducted on base of the standards of the product, process requirements and applications interactions with product, on base of the investigations a site investigation report is to be completed.
Site investigation assessment
Site investigation assessment is the solutions or compliance or the non conformity raised with the product or product quality defects are identified during the investigations at customer end applications and in processes, the responsible person is collecting the information form the site investigation report to assess further actions required. If the customer is agree to replacement of the product that actions are taken the same or others wise material claim can raised on material value. Responsible person conducting and keep the documentation, details of any corrective actions and preventive actions required at manufacturing processes to eliminate future defects in the product and maintain the quality products.
———————————————————————-
Download Formats in Word document | Excel Sheet | PDF Format
Download Site investigation Report
———————————————————————-